The device or materials that are used to separate unwanted gas, vapor, or other particles in the air are called filters. To ensure ideal quality conditions, to make paint application while taking into account the rules of employee health and environmental protection, filters should be selected carefully. Particles that bigger than 10 microns that can not be seen by the eye have negative effects on paint applications.
Intake filters ensure that the air taken from the atmosphere is delivered to the paint booth after filtered from particles that may negatively affect the application. Exhaust filters, on the other hand, ensure that overspray and other pollutants that are sprayed from the paint gun but not adhered to the part to be painted are caught before they are released to the atmosphere and fresh air is given to the outside.
In today's modern paint booths, we can examine filtration systems under two main headings as water wash and dry filter systems.
1 - Water wash Filter Systems
In such systems, overspray is caught in the area called waterfall which is located behind the paint application section. It has circulating water flow. Then the overspray is directed to the sludge separator system. The ambient air is directed to the section where the spray nozzles and air separators are located before it is exhausted. The air passing through there, containing overspray particles and other pollutants, is purified from these harmful substances by water curtains and moves to the exhaust chimney and is released to the atmosphere.
|
2 – Dry Filter Systems
Dry filter systems are used in the majority of industrial paint booths. In dry filter cabins, supply and exhaust filters consist of various filter materials. The main materials used in dry filter paint booths are as follows.
Synthetic / Polyester Fiber Filters:
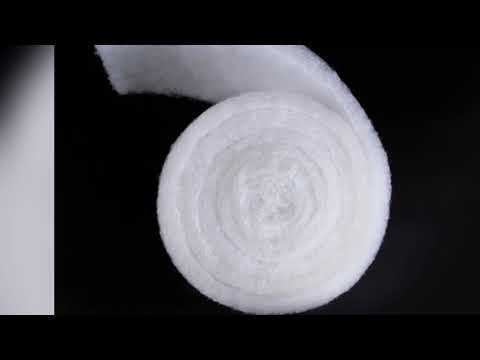
These filters are generally used for coarse filtration before high-efficiency filters. Their efficiency is not high, but they are positioned before higher efficiency and costly filters, increasing their life and retaining large particles. It can be used as a supply and exhaust filter.
Fiberglas Filtreler:
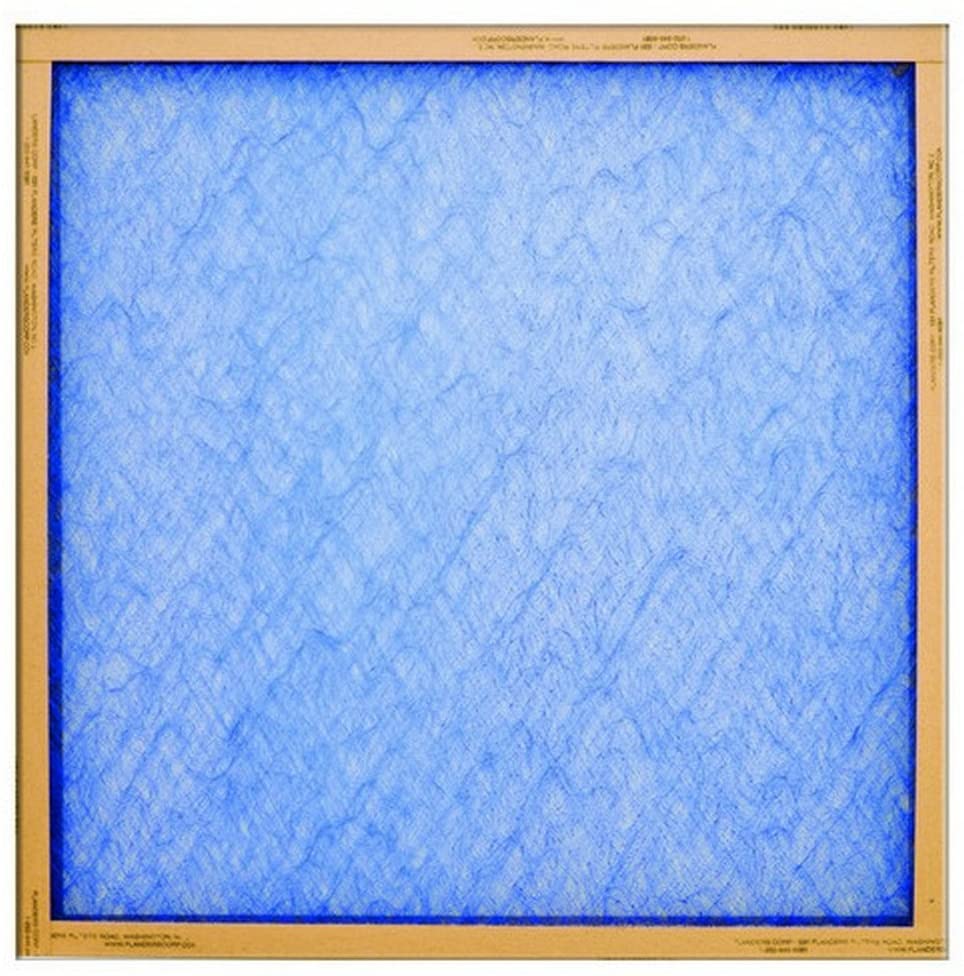
Since these filters are densified with continuous glass fiber fibers, they have a high retention feature. Fiber density increases from the air inlet direction to the air outlet direction. In this way, they exhibit high filtration performance.
Cardboard Separators:

It is used in paint booths to effectively contain overspray in liquid form. It is manufactured by pleating and gluing two layers of moisture-resistant cardboard. As a result of technological developments, there are now high-performance cardboard separators that hold more overspray. In this way, the filter change period is prolonged and the efficiency has increased.
Bag Filters:
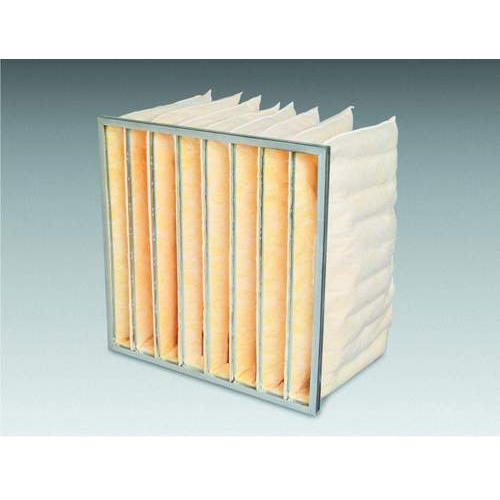
It is produced from high-quality synthetic filter material to be used after coarse filtration in applications requiring high efficiency by providing precise filtration. It is combined into small pockets made of synthetic fiber material for maximum efficiency.
Dry filters are divided into H, F, M, G classes according to the working principle and quality, from the highest quality to the most economical. While the G class represents coarse filters, the H class refers to high-performance Hepa filters used in places that require more precise air quality, such as operating rooms.
Dry filters can be used as single, double, or 3-stage depending on the frequency and method of use. For more precise results, 3-stage filters can be preferred to place Coarse (G class) first, then medium (M, F class), last fine (H class).
|
|
In dry filter booths, one of the easiest and most effective procedures for booth cleaning and overall efficiency is to routinely replace the exhaust and supply filters with new ones. With the differential pressure switches that can be placed on the front and back of the filters, you can understand the filter fill rate and confirm whether it is time for a replacement.
There are a wide variety of filters available in the market according to the usage area, efficiency, and price ratios. As Elsisan, we would be glad to share our experiences to help our customers make the most appropriate selection. You can transmit your questions and opinions by contacting us.
- Log in to post comments